Leveraging CNC Technology for Improved Electrical Performance in Copper Components
Copper CNC machining is an increasingly prominent approach in producing that leverages the exact, automated capacities of Computer Numerical Control (CNC) modern technology to create intricate parts from copper. Copper's one-of-a-kind residential properties, including superb conductivity, rust resistance, and machinability, make it a highly popular material in a selection of industries such as electronic devices, vehicle, aerospace, and telecommunications. The mix of copper's beneficial characteristics and advanced machining methods enables makers to create elements with high accuracy and decreased preparation, significantly pressing the boundaries of advancement. CNC machining enables complex geometries that would certainly be difficult or challenging to accomplish with traditional machining methods, making it excellent for the production of detailed parts, such as ports, heat sinks, and housings.The procedure of CNC machining entails the usage of a computer to control device tools for a more consistent and reputable result. Specialized techniques and tools are often employed to optimize the machining process, which can include utilizing reducing devices coated with hard materials to minimize wear and improve performance when functioning with soft metals like copper.
Discover copper cnc machining exactly how copper CNC machining merges sophisticated technology with sustainable techniques to generate intricate, high-precision components, driving innovation throughout sectors such as electronic devices, automotive, and aerospace.
Amongst the main advantages of CNC machining copper is the capability to generate complicated shapes that traditional machining techniques may not accommodate. The repeatability of the CNC machining procedure makes sure that mass production of copper parts keeps uniformity, thus fulfilling rigid market standards.
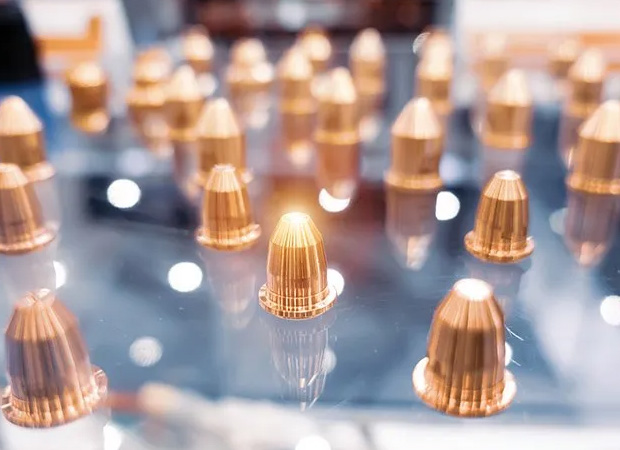
Temperature level administration plays an important role in the CNC machining of copper due to its capacity to carry out heat swiftly. High-speed machining can cause considerable heat generation, which might negatively affect the properties of the copper and aggravate tool wear. CNC machinists frequently turn to innovative air conditioning techniques, such as flooding coolant systems and haze lubrication, to manage warmth and expand tool life. By managing the temperature level during machining, manufacturers can accomplish better surface area finishes, improve accuracy, and generate parts with boosted mechanical residential properties. Additionally, with the development of technologies like high-pressure air conditioning systems and innovative reducing liquid formulations, CNC machining can attain optimal efficiency while properly taking care of thermal effects.
The sustainability facet of CNC machining copper is not to be ignored. Copper is a very recyclable material-- reusing copper requires approximately 90Discover countersink size chart exactly how copper CNC machining combines sophisticated modern technology with lasting practices to generate elaborate, high-precision parts, driving development throughout industries like electronic devices, automotive, and aerospace. much less power than mining and refining brand-new copper ore. CNC machining, combined with lasting practices, can lower waste by allowing makers to utilize scrap copper from various other processes. The assimilation of recycling and eco-friendly techniques into machining processes lines up with the significantly eco-conscious values of sectors and consumers alike. As companies make every effort to reduce their carbon footprint and enhance their ecological stewardship, CNC machining can play an important duty in promoting these goals by sustaining recyclable products circulation within the supply chain.
In enhancement to sustainability, cost-effectiveness is an additional essential variable for suppliers picking CNC machining for copper parts. CNC machining gives a decrease in labor prices due to its computerized nature and lessens the demand for considerable hand-operated treatment. In addition, for tiny to tool set manufacturing runs, CNC machining can verify a lot more cost-effective contrasted to standard machining processes, as it enables for seamless adjustments and design changes without extensive retooling.
As innovation develops, the functionalities within CNC systems are increasing, additionally enhancing the capabilities of copper machining. These simulations make it possible for far better preparation of tool courses and clarify exactly how the copper product will certainly respond throughout the machining procedure.
Competent machinists must be skilled in interpreting layout specifications, picking the suitable devices, and changing machining criteria to reduce concerns connected with copper's one-of-a-kind machining attributes. Hybrid machining, which integrates traditional CNC machining techniques with additive manufacturing, is emerging as a sensible technique for generating elaborate copper parts, blending the staminas of both technologies and possibly revolutionizing exactly how manufacturers come close to copper production.
In the world of r & d, CNC machining is aiding the expedition of new copper alloys to boost performance better. By synthesizing copper with products such as aluminum, tin, or nickel, manufacturers can engineer compounds that have enhanced strength, electric efficiency, and resistance to wear and deterioration. These innovations might lead to arising applications in sectors that depend greatly on conductive materials, such as sustainable power and electric cars. As international markets function toward higher energy effectiveness, copper's role as a conductor in digital circuits will remain critical, driving need for advanced machining remedies.
The aerospace and auto markets are likewise eager adopters of copper CNC machining, particularly where lightweight parts are of crucial significance. The mix of copper's light-weight nature and excellent electrical and thermal conductivity makes it a suitable selection for components such as electrical calls, warmth exchangers, and wiring systems. As the shift towards hybrid and electrical vehicles continues, the demand for high-performance copper parts will likely rise, thereby driving the demand for sophisticated CNC machining methods that make certain efficiency and quality in production. From a manufacturing viewpoint, the ability to innovate rapidly and deliver precision-engineered parts ends up being progressively necessary in taking on the arising needs of these fast-evolving fields.
As CNC machining innovation remains to develop, it permits further automation, where fundamental processes such as device adjustments, assessments, and upkeep can be set right into the manufacturing cycle. This development implies that producers will be able to attain greater performance degrees, shorter lead times, and greater flexibility in suiting personalized demands or variants in style. As a result, businesses that participate in CNC machining procedures are much better fit to pivot in reaction to the shifts in customer and market needs, promoting growth in an increasingly affordable landscape.
Discover countersink size chart just how copper CNC machining merges advanced technology with lasting methods to create intricate, high-precision components, driving technology throughout markets like electronic devices, auto, and aerospace.
The international market for CNC machining of copper is observing considerable development, influenced by variables such as the increase of clever innovations, electric automobiles, and ongoing initiatives to enhance power efficiency across numerous applications. In this skill, training and development development stay paramount; investing in labor force education on CNC machining strategies, innovations, and product scientific researches will encourage producers to remain ahead of the contour.
As industries develop and the limits of modern technology expand, embracing CNC machining's capacity will certainly be vital to realizing unmatched development and technology in the application of copper products. The synergy of copper's product buildings with advanced CNC machining methods advertises a brand-new age in which accuracy, sustainability, and efficiency work hand-in-hand to create innovative elements that will certainly specify the future of manufacturing and past.